Services
Since 1988, Vibro-Consult AG has analyzed the vibration of
more than 1200 machines and equipped more than 250 machines with new vibration monitoring systems.
Vibro-Consult makes this enormous experience available to its customers in the power plant and industrial sectors.
As an independent and certified company, the highest expectations for measurement technology and machine diagnostics can be met.
VC Fingerprint
(Machine diagnosis by means of vibration analysis)
It is a valuable input for the power plant to track the important power plant requirements. The VC fingerprint focuses on the following objectives:
- Get to know and assess the running behavior of the machine group in the entire load range
- assess the current condition
- determine the causes of abnormal behavior of the machine group
- make customized adjustments to the vibration monitoring system, taking into account the safety requirements, the running behavior, the standards and the operational situation.
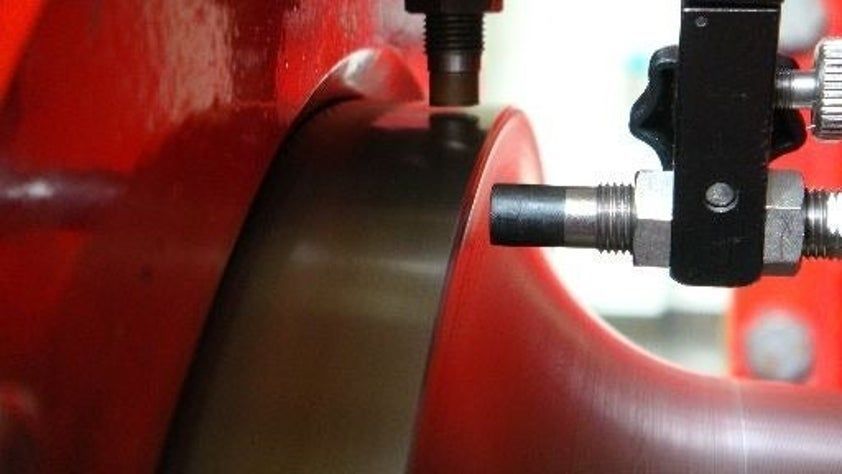
This service provides both the supplier and the operator with an independent assessment of the smooth running of the machine and documents it for both parties. This service is often used BEFORE and AFTER the inspection to obtain an optimal comparison situation.
We have listed 77 reasons to perform our fingerprint. You can find them here.
VC- Balancing
(Reduction of mechanical unbalance)
A very efficient and the best known way to reduce vibrations and forces on the machine. Here we are talking about, by means of suitable balancing masses:
- significantly improve the running smoothness of the machine
- reduce undesirable rotating forces that can unnecessarily stress bearings, bearing pedestals, the foundation, the structure of the rotor and housing, the piping, etc., and consequently lead to damage
- prevent bending of the shaft and thus reduce the risk of coming into contact with stationary parts
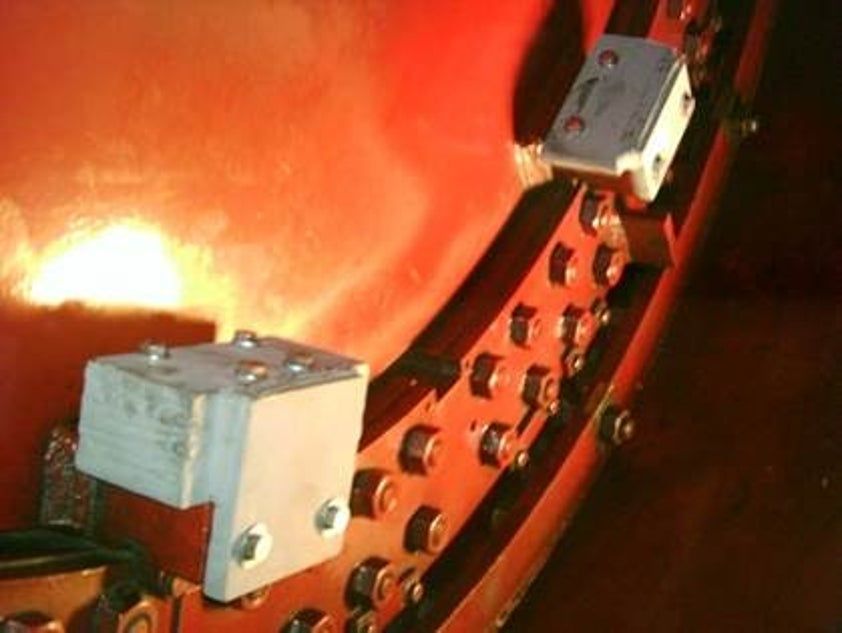
On the one hand, this process enables energy production that is gentle on the operation and, on the other hand, significantly increases the service life of the machine. With the balancing SW "VC-CAB" (Computer Aided Balancing) the best results can be achieved in this respect.
VC support during revisions/rehabilitations
Revisions of turbines and generators always mean a large expenditure of time and money. To ensure that everything runs as desired in the field of machine vibrations, Vibro-Consult AG offers support during the revision, which means:
- A basic VC measurement is carried out before the revision. This measurement serves on the one hand as a basis for the permitted vibration values after the revision and on the other hand as further support for the definition of the revision work to be carried out.
- During commissioning, Vibro-Consult is on site and monitors the machine behavior. In case of problems, immediate support is guaranteed and corrective measures can be taken in time.
- After the overhaul, a basic VC measurement is carried out again, thus proving the new vibration quality.
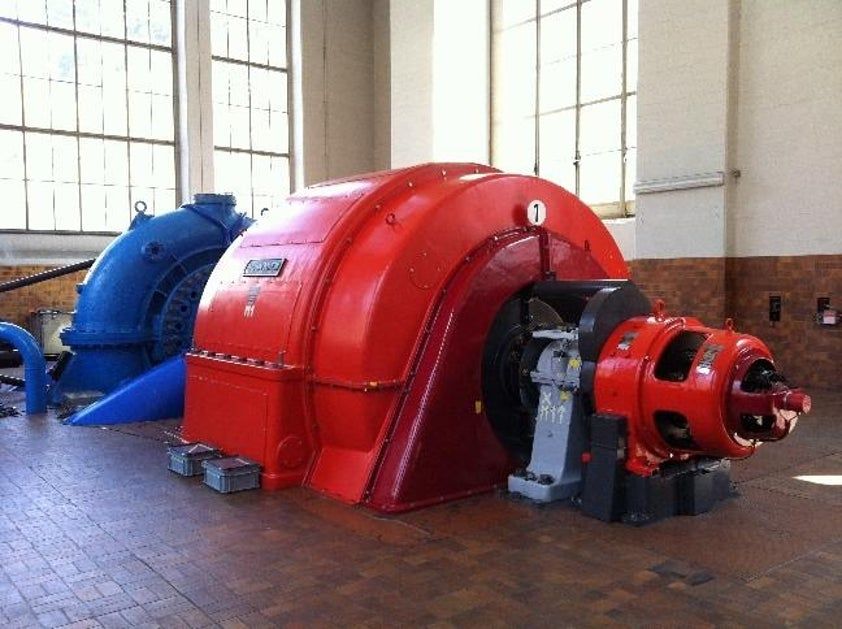
For both the supplier and the operator, this service evaluates machine smoothness from a neutral point of view and documents it for both parties.
VC Special measurement
The variety of challenges in a power plant always requires special measurements to procure the desired information. Vibro-Consult AG offers additional measurements such as:
- Torque measurements (contactless or by means of telemetry)
- Tensile measurements (by means of telemetry)
- Noise measurements
- Modal analyses
- Vibration measurements during blasting
- Winding head measurements, impact tests
- and much more
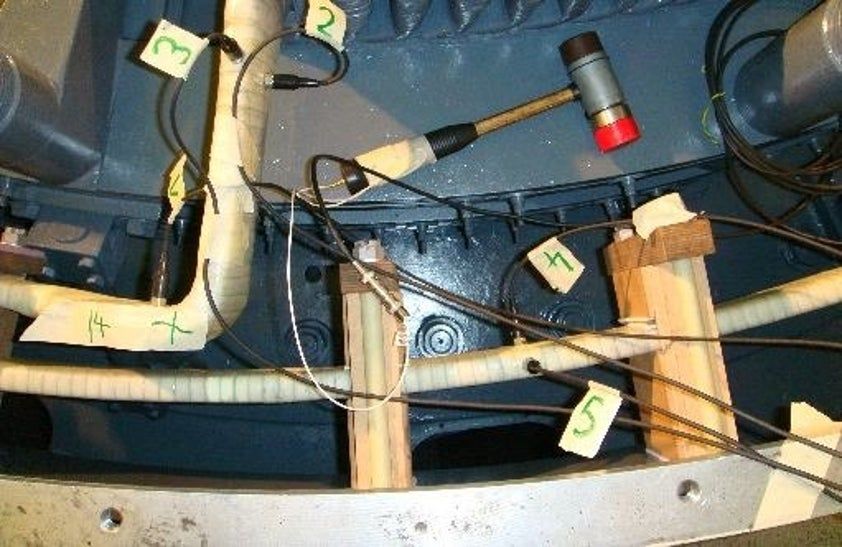
Periodic checks of the vibration monitors
Vibration monitoring is probably the most important mechanical protection of a rotating machine. This protective device - like other protective units - must be periodically checked for proper functioning. It is generally recommended to repeat these functional checks after 3-5 years. This ensures machine protection in the event of an incident and proves the maintenance obligation.
During the functional check of vibration monitoring systems, the functionality is checked from the probe to the machine triggering. On the one hand, it is ensured that the probes detect the vibrations correctly (a shaker is used as a simulator, for the relative as well as the absolute probes) and, on the other hand, the still active measuring range is checked (check of the linear measuring range by means of a micrometer).
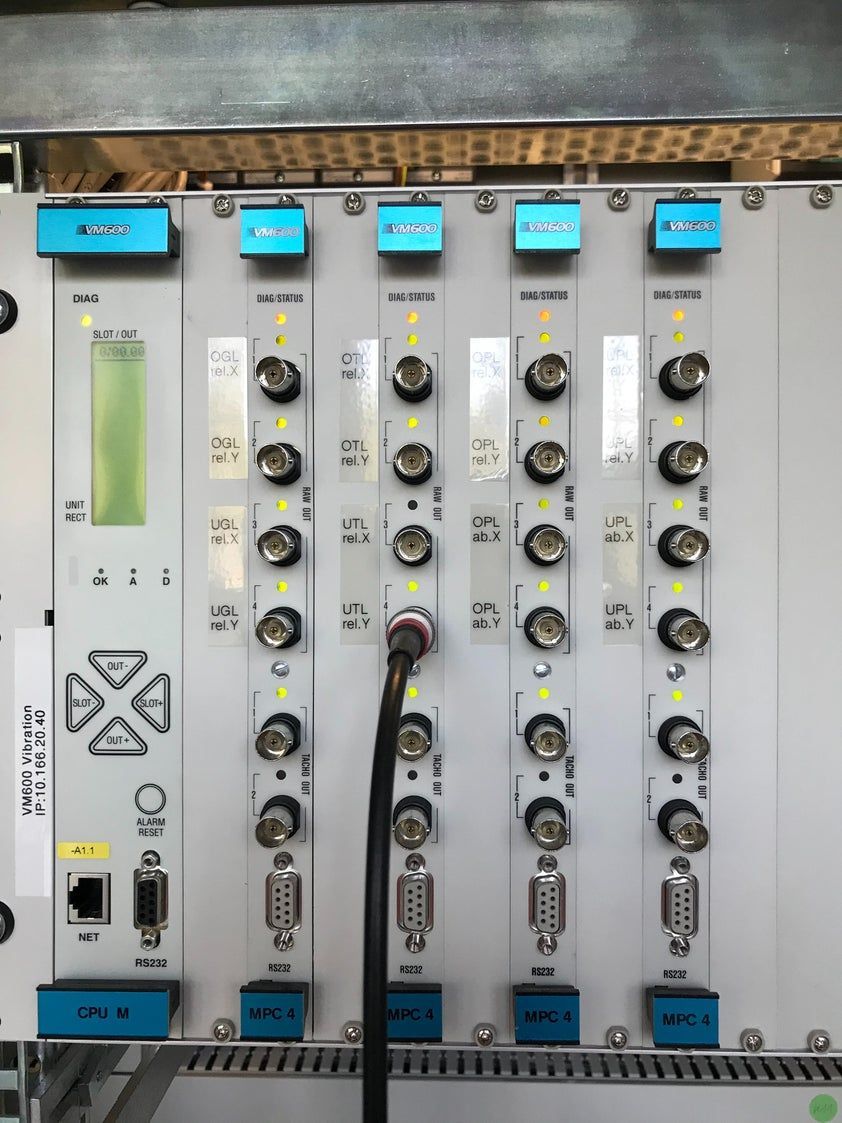
During vibration monitoring, it is checked whether the processing of the vibration information is processed according to the configuration (programming). For this purpose, the machine to be checked must be at a standstill. If necessary and in consultation with the customer, repairs, corrections and readjustments are made directly.
VC Trainings
Vibro-Consult AG conducts training courses for a better understanding of the topic "vibrations". Very popular are the 1-day trainings, which are held on site (i.e. at the power plant).
Training contents:
- General introduction: Vibrations
- Basic introduction: basic concepts of mechanical vibrations
- Possibilities of vibration monitoring
- Discussion of the existing installations
- Discussion of the setting possibilities (configuration)
- Practice on site
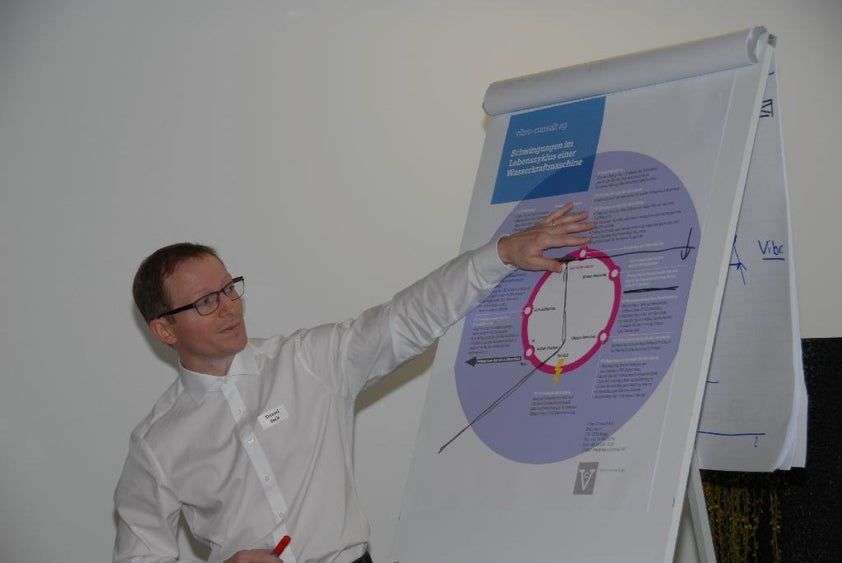
Who is this training for?
Basically, this seminar is suitable for all power plant employees who are involved in power plant operation. It is suitable as an introduction and as a refresher course. Further training courses are available on request.
VC Risk analyses
At a time when the demand for energy in general and electrical energy in particular is still unbroken and will continue in the medium and long term, the energy industry is faced with the situation of, on the one hand, creating new energy-generating plants, which are, however, becoming increasingly difficult to realize, and, on the other hand, continuing to operate existing plants as long and safely as possible.
Sensitivity regarding personal safety and plant security in today's information society is very high. In addition, there is an increased personal responsibility resulting from legal requirements (e.g. OR 663b).
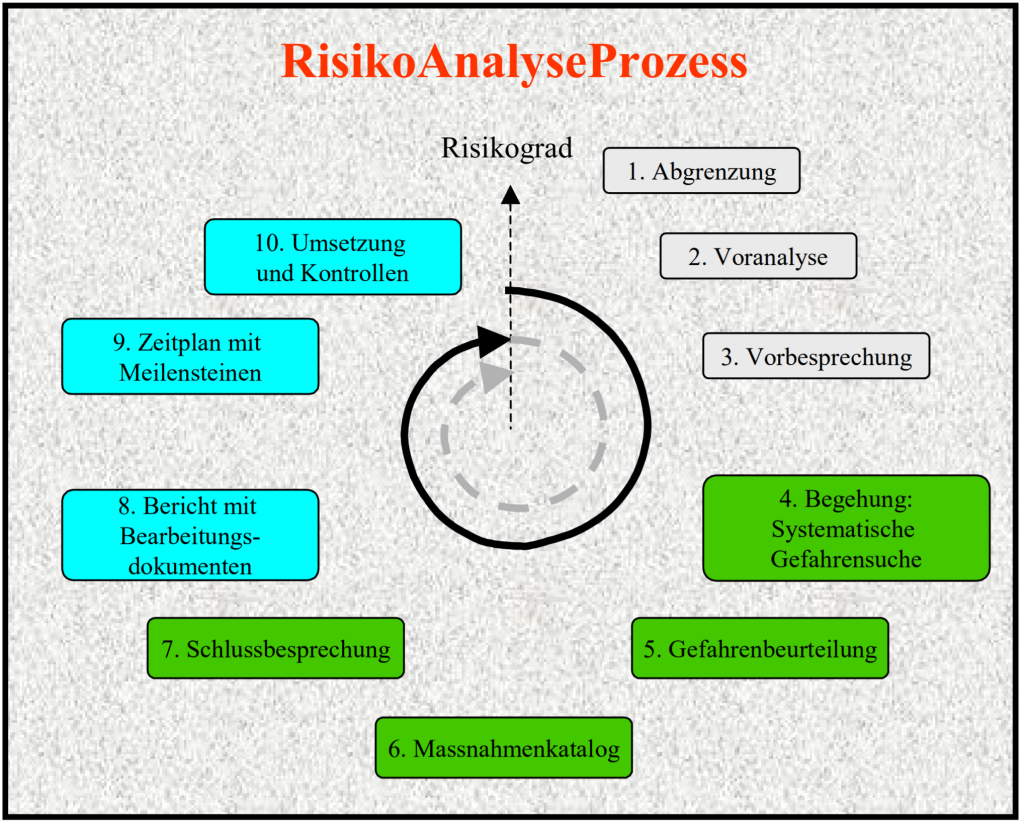
The risk analysis process shows the basic hazards of power plant operation and thus results in starting points for various optimizations. In addition to the individual risk-reducing measures, it is even possible to achieve a common safety standard across several power plants.